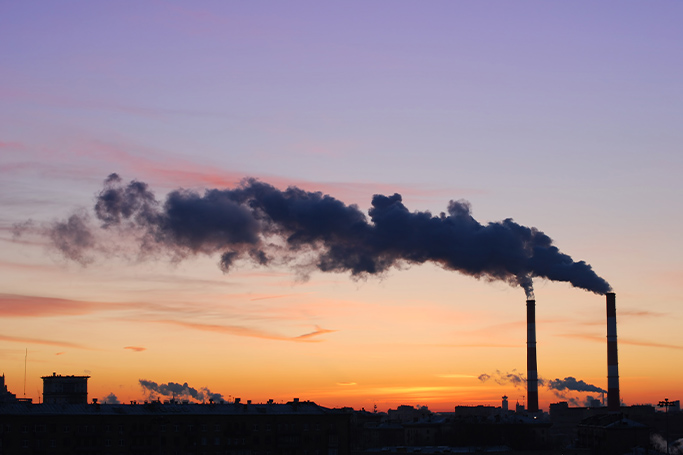
07.02.2023 | Tendencias del sector químico
Cómo ahorrar energía en la industria cerámica
Uno de los retos a los que nos vamos a seguir enfrentando durante este 2023 en el clúster cerámico de Castellón es la escasez tanto de las materias primas como de la energía. Como resultado, el coste del gas es tan alto que para muchos productores es difícil conseguir un margen de beneficio en la producción que les permita, al mismo tiempo, apostar por la innovación y cumplir con los objetivos de descarbonización de la Unión Europea. Por este motivo, la búsqueda de alternativas que consigan ahorrar energía durante los procesos productivos es una prioridad para muchas empresas del sector.
En este artículo nos centraremos en tres posibles opciones para ayudar a los productores cerámicos a lograr un mayor ahorro energético:
- Cómo ahorrar energía con la decoración digital mediante cabezales no piezoeléctricos
- Cómo ahorrar energía en las fases de molturación y atomización
- Cómo ahorrar energía reduciendo el espesor de las piezas cerámicas
No obstante, te invitamos a contactar con nuestro equipo técnico para estudiar otras formas de mejorar la eficiencia de tu proceso productivo con el uso de los aditivos químicos adecuados.
Cómo ahorrar energía con la decoración digital
Para hacer frente al hándicap del gasto energético, una de las opciones que te proponemos es la decoración digital mediante la inyección de esmalte de base acuosa con cabezales no piezoeléctricos. Esta opción, además de ser más sostenible, te ayuda a optimizar tu proceso de producción.
Mayor ahorro de energía gracias a los cabezales no piezoeléctricos
Si comparamos este tipo de aplicación con otros mecanismos de esmaltado como es el caso de la aplicación analógica mediante el sistema airless, encontramos grandes diferencias, siendo la más destacada la merma del esmalte
Y es que el sistema airless no distingue los límites de la baldosa al aplicar el esmalte, mientras que con la aplicación digital ajustamos el esmalte a la superficie de la baldosa. Por tanto, las mermas se minimizan.
Además, las ventajas de la decoración digital mediante cabezales no piezoeléctricos van más allá del ahorro energético. Al disponer de un alto sistema de automatización, se minimizan consumos y se reduce la supervisión del operario, favoreciendo el ahorro de recursos.
Por otro lado, la tecnología inkjet con cabezales no piezoeléctricos permite que el tamaño de partícula sea similar al del esmalte tradicional, gracias a lo cual se consigue un ahorro en el consumo de energía durante la molturación, con respecto a la aplicación digital de esmaltes que usan cabezales piezoeléctricos.
Para poder conseguir el ahorro energético comentado, así como la mayor sostenibilidad en el proceso, te recomendamos los productos de la familia DIGICER GL. Estos aditivos reológicos han sido diseñados especialmente para el esmaltado digital a través de sistemas no piezoeléctricos.
DIGICER GL permite utilizar una tecnología capaz de ahorrar energía y reducir el consumo de materias primas, dotando al esmalte de las propiedades reológicas más adecuadas.
Cómo ahorrar energía en las fases de molturación y atomización
A pesar de que la industria cerámica consume una gran cantidad de energía, especialmente gas, con los aditivos adecuados podemos reducir notablemente su consumo. Empezaremos estudiando cómo ahorrar energía en las fases de molturación y atomización, en las que el potencial ahorro de gas es muy destacable.
Lo esencial para mejorar el ahorro energético en esta fase del proceso es minimizar la cantidad de agua a evaporar. De este modo, no solo se reduce la energía necesaria para secar la barbotina, sino que también se aumenta la productividad. Esto sucede porque, al contener menos agua, se procesa más cantidad de sólido en el mismo tiempo.
Obviamente, si reducimos la proporción de agua de la barbotina, significa que su porcentaje de sólidos debe aumentar. Como sabes, existe un aditivo químico especialmente diseñado para esta función: los defloculantes, que permiten que la pasta cerámica adquiera las condiciones reológicas adecuadas con la menor cantidad de agua posible.
Los defloculantes se introducen durante la molturación de las materias primas cerámicas con el objetivo de obtener las condiciones deseadas de densidad, viscosidad y rechazo.
Si quieres conocer más a fondo cómo funcionan los defloculantes y qué ventajas tienen, te recomendamos este artículo donde lo explicamos en profundidad. A continuación, nos centraremos únicamente en sus beneficios respecto al ahorro de energía en la industria cerámica.
Ejemplo de ahorro de energía con uno de nuestros defloculantes
Para entender cómo la elección del defloculante adecuado reduce el consumo de gas en la industria cerámica, vamos a ver un ejemplo práctico con uno de nuestros defloculantes más recomendados: DOLAPIX ED 4957.
DOLAPIX ED 4957 es un tipo de defloculante basado en la acción complejante de cationes multivalentes floculantes, como son los iones Ca2+ y Mg2+, eliminándolos así de la doble capa difusa alrededor de las arcillas que componen la pasta cerámica. Estos cationes proceden de:
- El agua de molturación (aguas duras)
- La solubilización en materias primas en el tiempo de remanencia en las balsas previo a la atomización
Según las pruebas realizadas al añadir esta tipología de defloculantes (complejantes), con DOLAPIX ED 4957 se consigue aumentar de media la densidad a la viscosidad de trabajo.
Como hemos comentado, un aumento del contenido en sólidos de la barbotina supone una disminución de la cantidad de agua a evaporar y por lo tanto una disminución del consumo específico del atomizador (Kcal/Kg atomizado) y, por tanto, también un aumento de la producción.
En la siguiente tabla puedes ver de forma detallada la variación entre el contenido en sólidos inicial y el final y su respectivo ahorro energético. Por ejemplo, como se refleja en la tabla, para pasar de un 64 % a un 66 % de contenido en sólidos ahorramos un 9,3 % de consumo energético.
Contenido en sólidos final de la barbotina | Consumo | Ahorro energético (%) | ||||||
Contenido en sólidos inicial (%) | ||||||||
(%) | (Kcal/ Kg at) | 58 | 60 | 62 | 64 | 66 | 68 | 70 |
60 | 517 | 8,5 | ||||||
62 | 472 | 16,5 | 8,7 | |||||
64 | 431 | 23,7 | 16,8 | 8,7 | ||||
66 | 391 | 30,8 | 24,4 | 17,2 | 9,3 | |||
68 | 355 | 37,2 | 31,3 | 24,8 | 17,6 | 9,4 | ||
70 | 320 | 43,4 | 38,1 | 32,2 | 25,7 | 18,2 | 9,6 | |
72 | 290 | 48,7 | 43,9 | 38,6 | 32,7 | 25,8 | 18,3 | 9,4 |
Fuente: Ahorro energético en el sector azulejero, IPEAE.I.S.B.N.:84-7579-963-9
Precauciones
Hay que tener en cuenta que es necesario optimizar el defloculante para cada una de las pastas cerámicas. Y es que los defloculantes se deben utilizar en pequeñas proporciones, debido a que un exceso puede ocasionar:
- Viscosidades no adecuadas.
- Sedimentaciones rápidas
- Sobredefloculación, es decir, una adición excesiva de defloculante que termina produciendo un aumento de la viscosidad.
Por otro lado, también hay que tener en cuenta que la dureza del agua influye notablemente en la defloculación, así como la composición mineralógica de las materias primas.
Por todos estos motivos, es necesario realizar un estudio previo para valorar qué defloculante funcionará mejor en cada caso concreto. Puedes contactar con nuestro equipo técnico para que analice tus circunstancias y te ofrezca el producto más adecuado para ti.
Cómo ahorrar energía mediante la reducción del espesor de las piezas cerámicas
Es lógico que trabajar con piezas más delgadas te permitirá ahorrar no solo energía, sino también reducir el consumo de agua y de materias primas. Pero, como inconveniente, durante la fase de fabricación la cerámica tiene menor resistencia mecánica, por lo que se puede romper más fácilmente.
Te preguntarás, por tanto, si existe alguna forma de obtener los beneficios de las piezas finas sin renunciar a una alta resistencia mecánica. Afortunadamente, la respuesta es sí y te vamos a enseñar cómo.
Ahorro energético y ligantes temporales
Para empezar, existen aditivos cerámicos que evitan que las piezas se rompan o dañen a mitad del proceso productivo, una de las fases más delicadas para las piezas finas. Y es que una vez ha finalizado el proceso de producción incluso la cerámica más fina tiene unas excelentes prestaciones técnicas a pesar de su menor espesor.
Concretamente, podemos aumentar la resistencia mecánica de las piezas cerámicas gracias al uso de ligantes temporales. Su principal característica es que endurecen la pieza pero únicamente en la fase de precocción. De este modo, la protegen de posibles daños y facilitan su manipulación, evitando que se rompa.
Para lograr este efecto, los ligantes temporales crean una retícula gracias al cual las partículas cerámicas se unen de forma homogénea. Así la pasta cerámica obtiene una mayor resistencia mecánica pero mantiene su flexibilidad.
Es necesario destacar que, como es natural en un proceso productivo con tantas variantes como el cerámico, no todos los ligantes temporales son recomendables para todas las circunstancias. Por este motivo, es importante estudiar en profundidad cada caso y usar el producto adecuado para cada situación.
No obstante, queremos ofrecerte una visión global de la situación y que comprendas el funcionamiento y beneficios de este tipo de producto a la hora de lograr un mayor ahorro energético. Por este motivo, en este artículo te presentamos algunas de las familias de productos más habituales y te recomendamos contactar con nuestro equipo técnico para ayudarte a buscar la solución más adecuada para tu caso concreto.
Cómo ahorrar energía en la industria azulejera
Nuestra familia de productos más recomendada para pavimento y revestimiento cerámico es la gama TENACER. Esta línea de productos no solo da buenos resultados en los ciclos de producción habituales, sino que está especialmente indicada para la producción de baldosas de gran formato.
Gracias a los productos TENACER, la baldosa adquiere una alta resistencia mecánica en seco, lo que permite reducir de forma notable el espesor de la pieza.
Cómo ahorrar energía en el sector sanitario
Fuera del sector azulejero también son cada vez más deseadas las piezas finas, especialmente en la industria de sanitario. Entre los productos destinados a esta última, destaca OPTAPIX AC 40. Este se combina con agua para que forme una película alrededor de las partículas que provoca el pegado entre ellas. Su gran efectividad se debe a la formación de fuerzas cohesivas entre las partículas cerámicas.